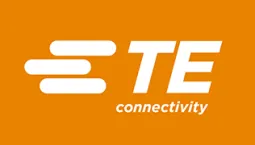
Safety critical welds in vehicle airbags


Solution
- Motorised tensile test stand
- Digital Force Gauge
- Software for data export to SPC analysis system
Benefits
- Simple reliable and repeatable test procedure
- Rapid test turnaround for constant batch monitoring
Requirement
The customer required an easy-to-use system for production staff on the factory floor. Testing needed to be carried out in the minimum amount of time with very little training. The test was required for the connector used in the deployment of car airbags. Rigorous batch testing was necessary as defects have serious implications for safety.
The welded portion of the connector was pulled to destruction at a constant speed to ensure the best repeatability for results. Data needed to be easy to transmit to the company's SPC (Statistical Process Control) software on their network.
Solution
A lower gripping fixture ensured that the operator could instantly fit the airbag connector. A rear locating lug on the connector was pushed into a recess in the fixture with the body of the connector held in place by spring-loaded clips. The upper gripping fixture had a lateral slot into which the connector strip was placed. A toggle clamp at the front of the fixture allowed the operator to quickly secure the strip, ready for testing.
The connector strip was pulled at 250 mm/min until break. The maximum tension force was recorded on the PFI and then sent to the software. The operator presses the release stud to open the spring-loaded clip at the end of the test, thereby allowing the connector to be quickly removed. The simplicity of this system and the ability to perform rapid testing provided the customer with a complete testing solution.
Test equipment
- UltraTest Motorised Test Stand (superseded by the MultiTest-dV series)
- PFI Digital Force Gauge 200 N (superseded by BFG Basic Force Gauge)

